Case study:
Custom data collection app for field inspections
If no one’s going to use an app, it’s not all that useful.
A national substation inspection company, responsible for capturing a wide variety of field data, was still relying on paper forms and tedious processes. The company’s technicians lugged around clipboards with stacks of forms, gathering critical reliability information, only to spend evenings in hotel rooms uploading photos, hand-entering the same data and labeling test samples collected earlier in the day. Luckily, the inspection company implemented a data collection app. But … no one wanted to use it.
Challenge
This inspection company is not a one-size-fits-all kind of operation. Rather, it’s an industry leader that offers highly specialized maintenance and reliability testing and services for the niche power system space. High voltage equipment, industry and location-based safety protocols, complex test packages, infrared and visual inspections – it’s a ton of data to collect and organize, not to mention transmit to testing laboratories, customer portals and other platforms.
Adopting a tablet-based inspection app to make data collection and transfer easier seemed like a no-brainer. Unfortunately, the first attempt proved more difficult than expected and left the inspection company with an app no one wanted to use.
“The first app built for us failed miserably because it did not align with our processes,” said Lee, the company’s field technician supervisor. “The app developer made incorrect assumptions about what we did and that led to a platform that frustrated, rather than helped, our team.”
Technicians would only use this app if it:
-
Gathered everything (machine readings, equipment photos, geographic locations, etc.) without paper forms
-
Easily transmitted data to the internal systems and customer databases
-
Eliminate data or reporting errors that would necessitate returning to an inspection site
-
Was easy to learn and use (many technicians did not have a lot of digital know-how)
-
Made the inspection process faster and simpler
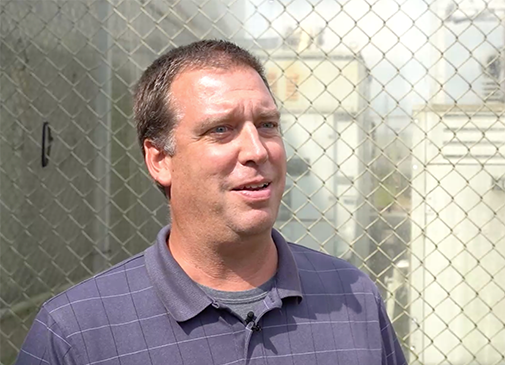

– Lee, Field Technician Supervisor, Substation Inspection Company
Our field staff went from saying they didn’t want to use an app to now being upset if they can’t use our app.
Method
The inspection company commissioned On Now Digital to develop a custom app. The first step in our approach? Gather all of the steps in the inspection and reporting process. Every single step. Sure, our experience in the utilities sector helped, but our team did not make assumptions.
“On Now Digital listens,” said Lee. “The software engineers sought to understand what we were trying to do rather than tell us what they thought we should do.”
Defining requirements before diving into a solution resulted in an app that was exclusive to the company’s specific process, helping the team to gather and report on oil samples, temperature measurements, nameplate photos and other data. All through one platform during a single site visit.
Impact
Through this software, the inspection company gained:
-
Efficiency. What used to take hours in data entry and sample labeling now takes moments with digital forms and barcode scanning.
-
Convenience. Instead of fumbling with clipboards and paperwork, technicians take only their tablets and testing equipment to sites.
-
Continuous improvement. Because On Now Digital has an ongoing relationship with the client, technicians can share feedback on the app and we can modify features as the business evolves.
Takeaways for your business
Trust on On Now Digital to:
-
Gather the information critical to your operations before building a solution
-
Balance technology with business know-how
-
Continue to refine your app after it’s been deployed
