Case study:
Custom system integration for fluid testing laboratory
Because off-the-shelf software doesn’t fit. And shouldn’t have to.
An Ohio-based fluid testing laboratory, the largest of its kind in the world, was shopping for a new laboratory information management system (LIMS) to track samples, produce workflows and transmit data reports. Just one problem: nothing on the market seemed quite right for the lab’s internal processes and high-capacity needs.
Challenge
This feeling wasn’t new. Back in 2008, the lab had found it just as challenging to select a LIMS platform that fit. After ruling out several off-the-shelf LIMS options, the company chose a financial software package and customized it to fit the laboratory. Sure, this LIMS substitute had some deficiencies, but it was better than a pen-and-paper tracking system, so it worked.
Until it didn’t. After 20 years, the software began to impede the lab’s ability to be efficient. Roadblocks included:
-
Inability to timestamp and track samples
-
Limited data collection and reporting functionality
-
Expensive maintenance and support
-
Lack of scalability
The lab defined what it needed in a system and launched a search for a new LIMS in 2018, but none of the existing LIMS platforms met the requirements. What to do, what to do.
The new software needed to:
-
Integrate with barcode software, company databases and other internal systems
-
Improve accuracy and efficiency
-
Accommodate the lab’s growth plan (increases in number of facilities, test parameters and sample volume)

On Now Digital was very good at getting into the trenches with us to define functional requirements – what do we really need this system to do, not based on how something has worked in the past.
– Jason, Director of Diagnostic and Analytical Services, Commercial Laboratory
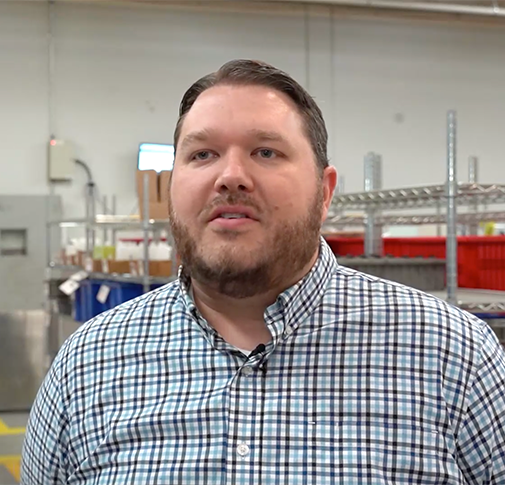
Method
The lab asked On Now Digital to pitch a custom solution. Our experience in the power system industry and familiarity with fluid testing laboratories added immediate value because our team understood fundamental processes and objectives.
“The On Now Digital team asked the right questions to look at the current ways we work and identify different, better ways to get things done,” said Jason, the lab’s director of diagnostic and analytical services. Jason noted that other LIMS software companies wanted to prescribe a solution and expected the lab to adapt its processes to their systems. The On Now Digital approach was drastically different.
In 2019, the lab selected a LIMS system that most closely fit its needs and engaged On Now Digital for a substantial custom optimization. We have remained an ongoing partner, continually improving the platform based on our client’s feedback and growth.
Impact
Through this true process-based integration, SDMyers the lab has:
-
Gained productivity. What used to take days now takes hours. The integration eliminated the hand-transcription of data, boosting accuracy and allowing the reallocation of staff to other tasks.
-
Saved money. SDMyers The lab has greatly reduced investments in tech support, refocusing on system improvements rather than system survival.
-
Improved the quality and availability of knowledge. Lab team members know exactly where samples are in the process and what is expected regarding testing and reporting.
-
Positioned itself for growth. SDMyers Our client is better equipped to attract new customers and open new laboratories.
Takeaways for your business
Trust on On Now Digital to:
-
Collect, reformat and import data across disparate platforms
-
Evaluate critical integration points
-
Streamline workflow, productivity and reporting
-
Become an extension of your IT team
